Background
Challenges and Opportunities
For big Oil & Gas players, a large fleet size, and customer base creates umpteen operational hassles. Our client needed automation to improve its supply chain. The challenges they faced were:
No Real Time Data
Their Point-to-Point connected systems at times failed to provide real-time data to stakeholders.
Significant Operational and System Silos
Caused inefficiencies and delays
Shifting Away
From point-to-point integration system to hub & spoke.
Lack of Automation
The other significant issue confronting our client was the need for its customers to coordinate telephonically to procure the information on orders they have placed; thus, they wanted automation.
The issue of Bill of Lading (BOL), and Delivery Ticket
The generation of BOL/ DT at multiple locations demanded that they be updated into the application, manually, and on multiple occasions. The lack of automation resulted in the generation of irrelevant and erroneous data, along with undesired delay.
The seamless integration of various facets of the business to deliver a superlative user experience is the need of the hour.
Our Solution
The rigorous due diligence on the client’s business model and operations facilitated efficient customization of technological solutions. Techment created novel solutions on many fronts:
- Hub & Spoke:
- DIH: We executed a selective transition from point-to-point integrated systems to Data Integration Hub(DIH). It facilitated the sharing and synchronization of data between different applications.
- Sales Analytics: Our centralized platform brought various systems together, thus garnering data which would help our client optimize sales and customer experience.
- Scalability & Governance: DIH had a scalable cloud repository for data and file storage. This offered agility and governance benefits in the long run.
- Automating BOL & DT: Our self-service solution facilitated customers to directly see their Delivery Tickets and BOL’s in their E-Comm account.
- Blob Storage: To better leverage DIH, we facilitated the creation of a dedicated storage for fulfilled orders and other data.
- Event-Driven Integration: It allowed for real-time availability of data and reduced cost of manual efforts.
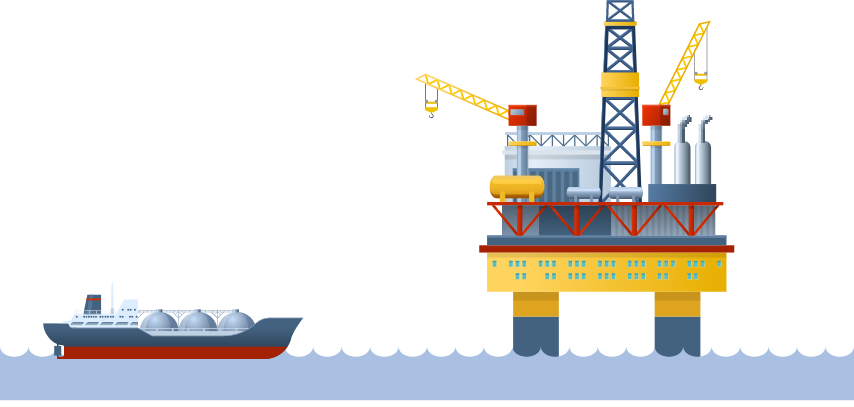
Technology Stack
Technology
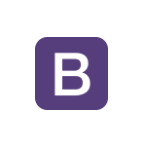
Bootstrap 3
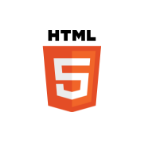
HTML 5
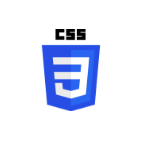
CSS3
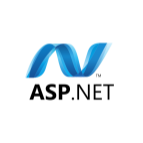
Asp.Net
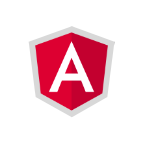
AngularJS(1.5)
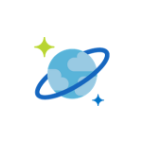
Azure-CosmosDb
Platform
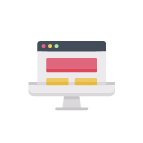
Web/Desktop
Impact & Business value
Our work with a major US player in this industry testifies that crafty use of technology & automation can go a long way in lowering costs, augmenting operational efficiency, and building proper software architecture to lay the foundation for meeting standards of Industry 4.0. Here are some of the areas that experience direct value creation:
Real-time operational visibility
Better data and cyber security
Better cost-efficiency
Better Customer experience with transparent process status and billing
Faster operations with process automation
Easy Scalability with microservice architecture
Lower silos and better systems integration